
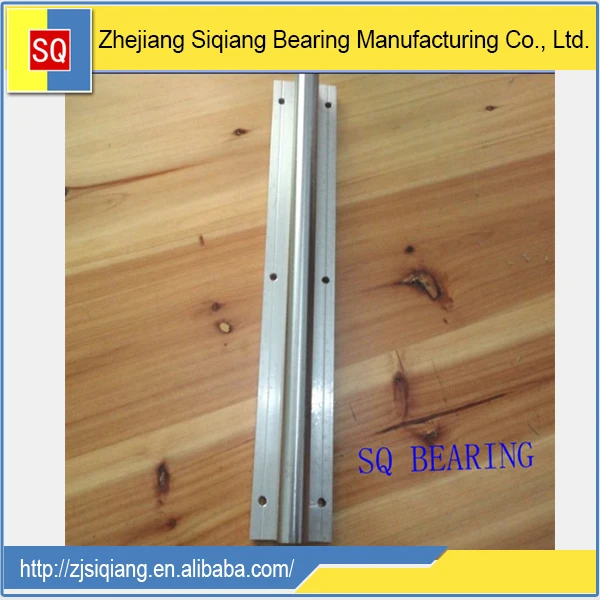
It’s really simple to test too, all you have to do is attach a dial indicator to the head and move it back and forth along the length of the machine. That is any machinist’s most important number.
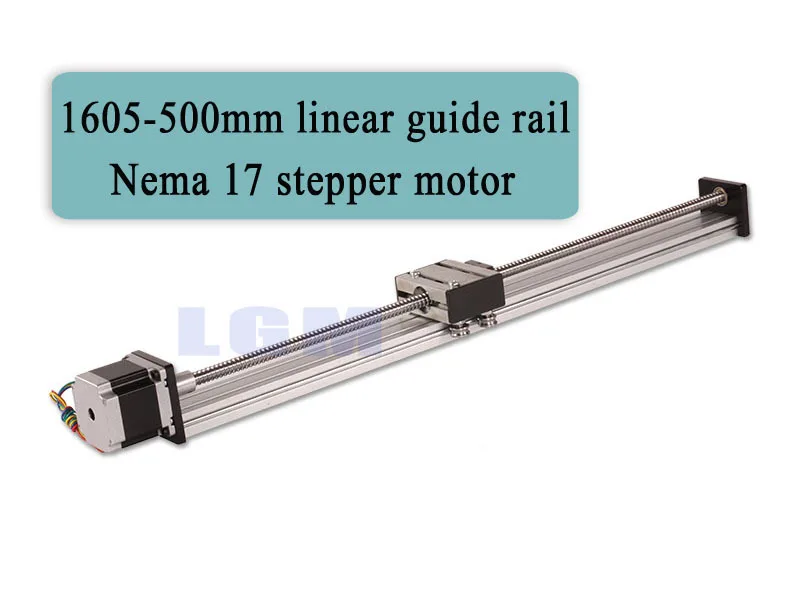
Many hobby companies sell them for thousands without any measurements on repeatability. The ideal machine is still a hard concept. This makes it easier to determine the actual quality of hobby machines and figure out the best route to take for your particular application. It would be nice to find out the repeatability measurement in everyone’s machine. I always watch the test runs to see how fast and consistent their cuts are, however this has been done many times and I think it’s time the community gets solid statistics on these machines. Posted in cnc hacks Tagged 8020, ball screw, extruded rail, mill Post navigation Below you can see the mill cutting out the Hackaday logo: We could highlight some other mill builds or 3d printers, but instead we think you’ll enjoy an extruded rail robotic bass guitar. We see this extruded rail used all over the place. He may end up bolting the base to the floor once all is said and done.
#CNC RAILS FULL#
For now he’s not running the motors at full speed because the vibration starts to make the table shake. He machined his own mounting plates to which those are attached.
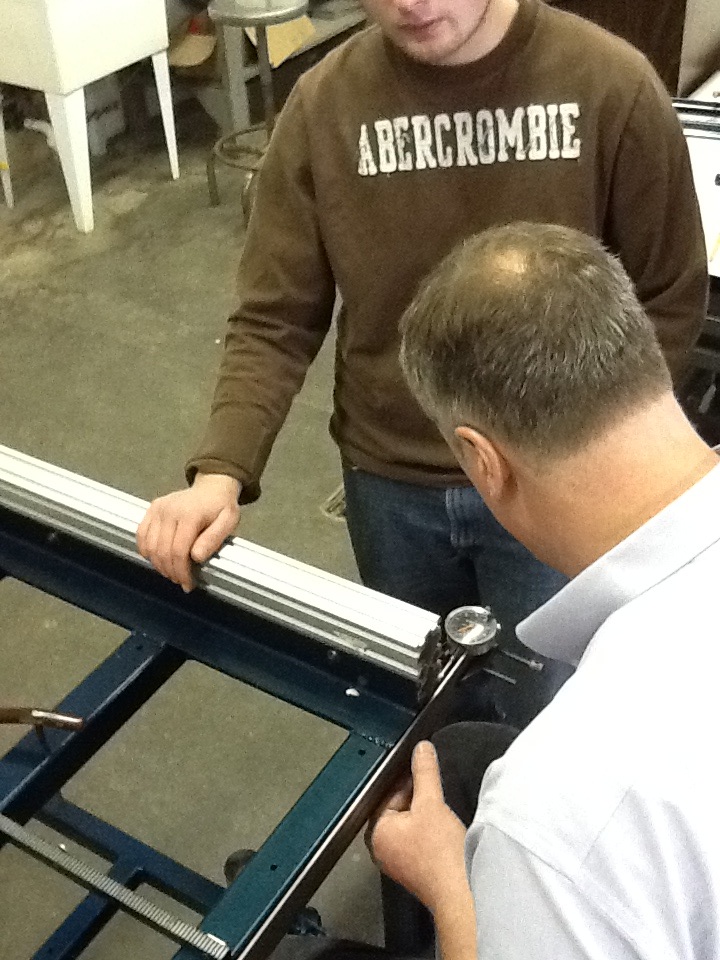
The X axis travels along a set of precision rails instead of precision rods. Two of them drive the X axis with the third moving the cutter assembly along the Y axis. He picked up the set of three ball screws on eBay for $180. He took this mill from start to finish in just two weeks. That’s not to say that we think is average. But using 80/20 brand extruded rail optimizes most of the build process into tasks manageable by the average basement hacker. There’s still quite a bit of machining that goes into a CNC mill build of this size.
